How can commercial solar customers be assured their system will perform as described? SunPeak's quality-driven solar commissioning process ensures our customers' systems meet or exceed established safety, reliability and performance expectations for the life of the system.
SunPeak systems are designed to comply with all standards established by the National Electrical Code (NEC), the local inspectors, and the leading solar equipment manufacturers that source the components used in our systems. Once a solar PV system has been constructed, SunPeak executes a rigorous commissioning plan that addresses any safety or equipment performance concerns before the system goes into full operation for the customer.
SunPeak's commissioning process consists of the following stages:
Installation Verification
The SunPeak commissioning team first visually confirms that all installed components are consistent with the project drawings and specifications. This includes checks on solar modules, inverters, and racking, overcurrent protection devices, wiring, and all monitoring equipment.
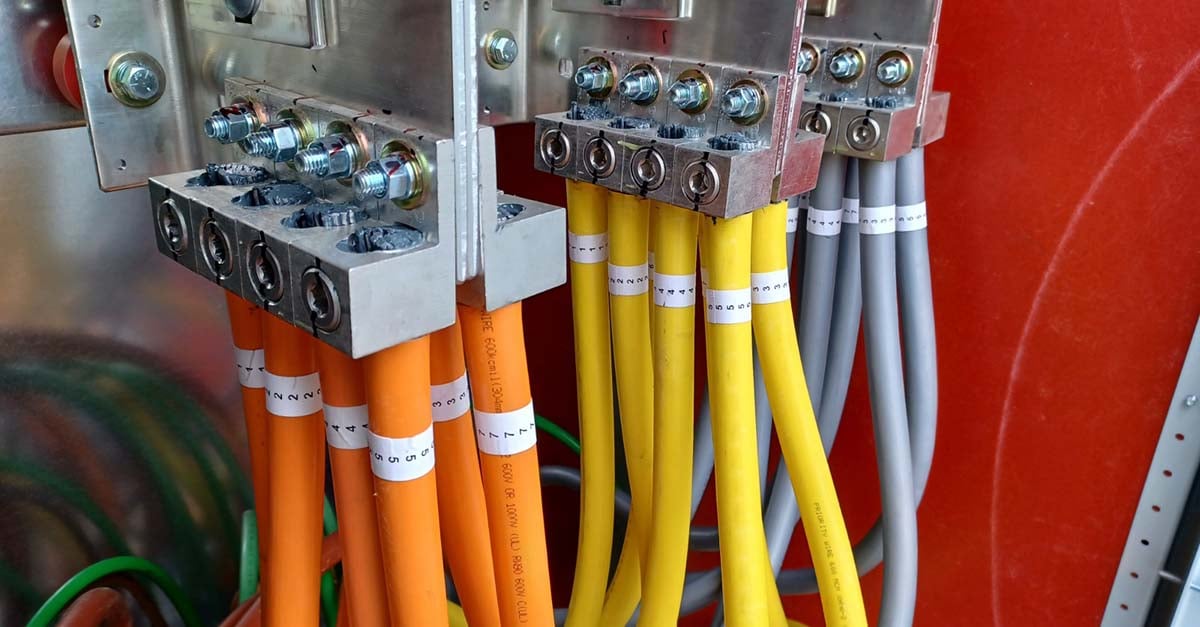
Quality Inspection
In addition to verifying the correct parts were installed, the commissioning team ensures the installation quality meets all required electrical codes and safety standards. Each part of the system is inspected to identify and flag any issues that do not meet the highest standard of workmanship. Any flagged items are documented and reported to the installation team for remediation. By proactively addressing potential issues that may affect the safe operation of the system over its lifetime, the commissioning process provides better value for customers and makes subsequent third-party inspections of the system more efficient.
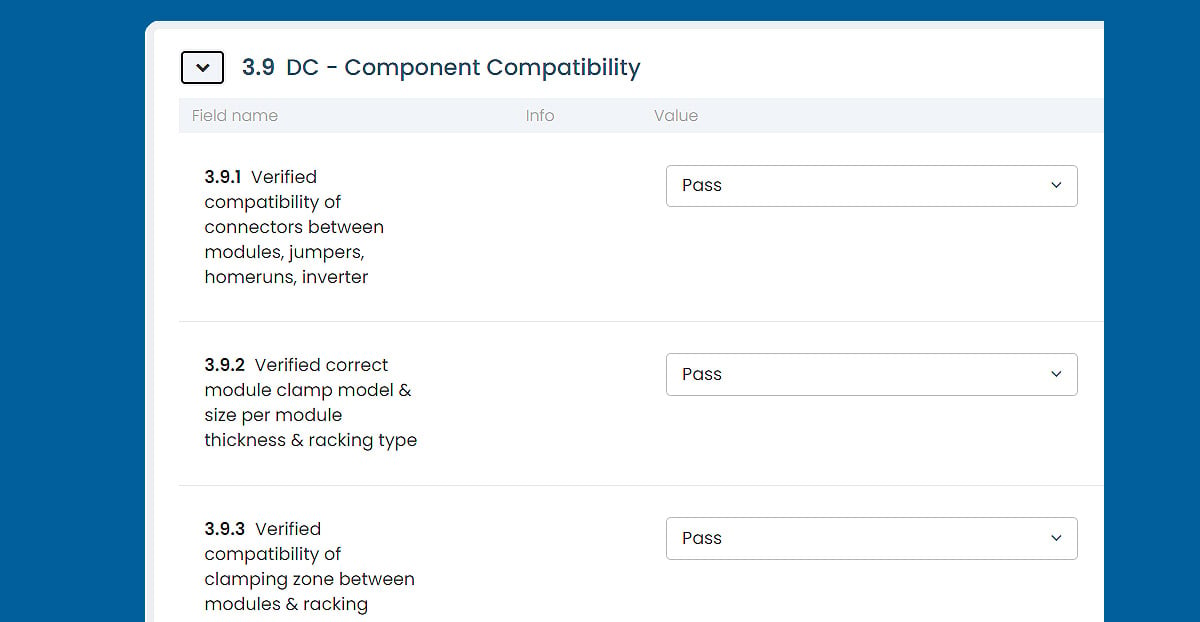
Above: As the installed system is inspected for final commissioning, SunPeak solar technicians will test, measure, and document a system checklist of more than 175 items to be included in the commissioning report.
AHJ Review
Upon passing all of SunPeak’s internal quality inspections, the system will be inspected and verified by the local Authority Having Jurisdiction (AHJ). This may include electrical, fire, and seismic inspections, depending on local requirements. These inspections are coordinated and documented by SunPeak as a prerequisite to obtaining utility approval to operate the interconnected solar PV system.
System Testing
In addition to visual inspections from SunPeak and local municipalities, each part of the PV system must be isolated and tested to demonstrate proper operation. Insulation on electrical wiring is tested for defects that could lead to short circuits or ground faults. Solar panels are tested with an I-V curve tracer that graphs the panel’s performance to verify its power output against its nameplate rating. Voltages are read at each electrical component to ensure they will operate within the correct voltage range. Circuit breakers and disconnects are tested to confirm the correct circuits will de-energize in the proper timeframe when exposed to the rated current levels. The baseline data from these tests is documented in a commissioning report that is provided to the client once the project is completed. In the event of a future warranty claim, these commissioning test results demonstrate the equipment was installed properly but no longer performs to the manufacturer warranty standards.
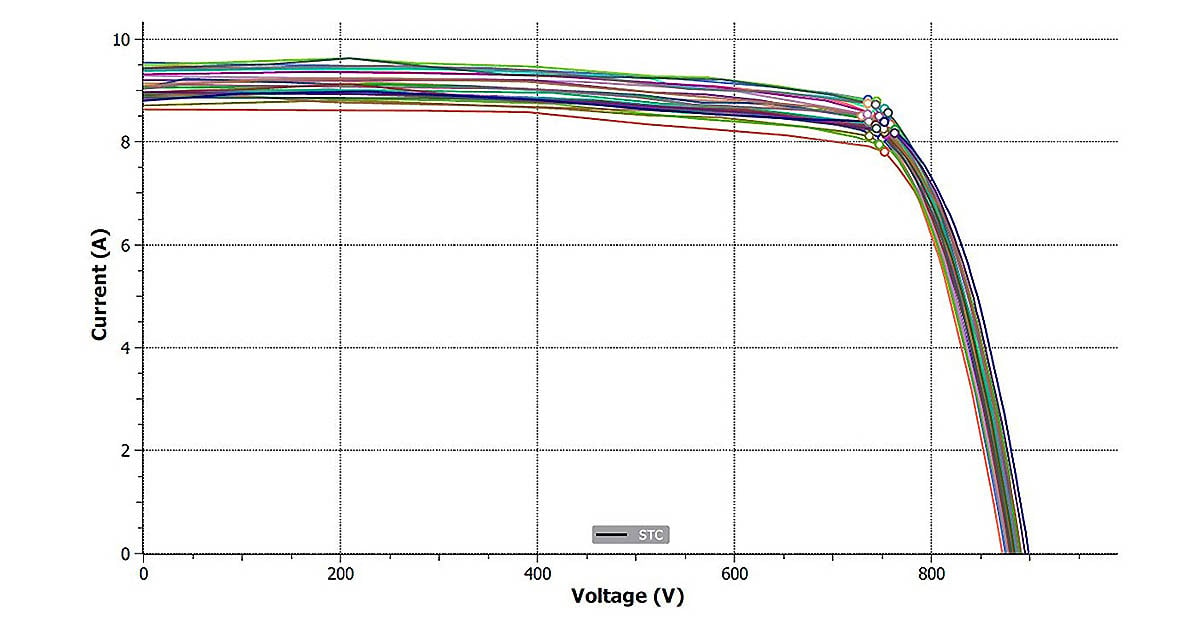
Above: An I-V curve (or current-voltage characteristic curve) is produced for each solar panel in the system so onsite solar technicians can verify the installed performance and efficiency of the panel falls within the rated capacity identified by the manufacturer.
Performance Verification
After each portion of the system has been inspected and tested, the entire system undergoes performance verification testing. A model calculates how much power or energy should be produced based on equipment specifications and assumed energy losses at each point in the system. This calculation is adjusted based on environmental conditions measured during the test period, primarily the available sunlight and the temperature of the solar panels. The actual power or energy output is measured or displayed with electrical metering equipment. By comparing the theoretical expected output with the actual output, the resulting Performance Ratio can be used to assess the system’s performance.
Expected System Output | 31.37 kW | Performance Ratio | 97.5% | ||
Actual System Output | 30.59 kW |
In some cases, SunPeak utilizes drones to conduct a thermal scan of the PV system during operation as another means of verifying its performance. The drone carries an infrared payload that measures slight temperature differences to produce a heat map of the solar array. Special software analyzes the heat map to diagnose potential problems with the solar panels and quantify how much energy may be lost. Drone thermal imaging represents the ongoing innovation in technology that continues to enhance the solar commissioning process.

Above: By taking an aerial thermal scan of the installed system using a drone, performance issues with specific solar panels can be quickly identified and addressed, especially in larger systems.
Utility Approval
The final step before the PV system can be energized is to obtain Permission to Operate (PTO) from the utility company serving the project site. Each utility is different in their interconnection requirements and commissioning processes. Utilities rely on the local AHJ inspectors or their own field engineers to verify that the system was installed according to code and meets the design submission. As part of their inspection, they will confirm the system has the ability to both quickly cease power transmission to the grid and also remain offline in the event of a utility outage, thus allowing their personnel to safely work on power lines without risk of back feed from solar generation. Labeling requirements will also be checked so that anyone accessing the solar equipment has proper information. During this visit, a bi-directional meter is often installed by the utility to credit the client when excess solar power is sent back to the utility. System approval is granted once the utility has fully verified the installed system is consistent with the utility’s expectations.
Customer Training
With the final utility blessing in hand, it is time to "flip the switch" and deliver a fully commissioned PV system to the client. This does not mean, however, that the customer is on their own with their newly commissioned power plant. SunPeak provides an orientation session for any members of the customer’s staff who may be involved with the PV system. This typically includes building owners, facility maintenance and IT personnel, and project financiers. The orientation covers basic training so the group understands the equipment that was installed, how to safely interact with the system, and how to access the solar monitoring platform.
SunPeak also provides a turnover document binder, an index of all documentation related to the project, including permits, warranties, test results, drawings, equipment manuals, and contact information. This information is essential for future reference if any maintenance or equipment replacement is needed.
Quality in Commissioning, and Beyond
Each step in SunPeak’s commissioning process has been carefully designed and managed to ensure customers receive a high-quality, safe, and reliable solar system that has been fully tested and approved. After the system is commissioned, SunPeak continues to provide seamless operational oversight and support for customers through its Operations & Maintenance (O&M) program. This service includes weekly monitoring checks, warranty claims management, notification of system errors, coordination of repair work, annual reporting, and additional customer training on basic preventative maintenance.
Proper system commissioning provides solar customers with peace of mind and the benefit of having less day-to-day upkeep of their system. By enlisting ongoing support with SunPeak's O&M program, customers realize their return on investment while focusing on running their business.